Products製品情報
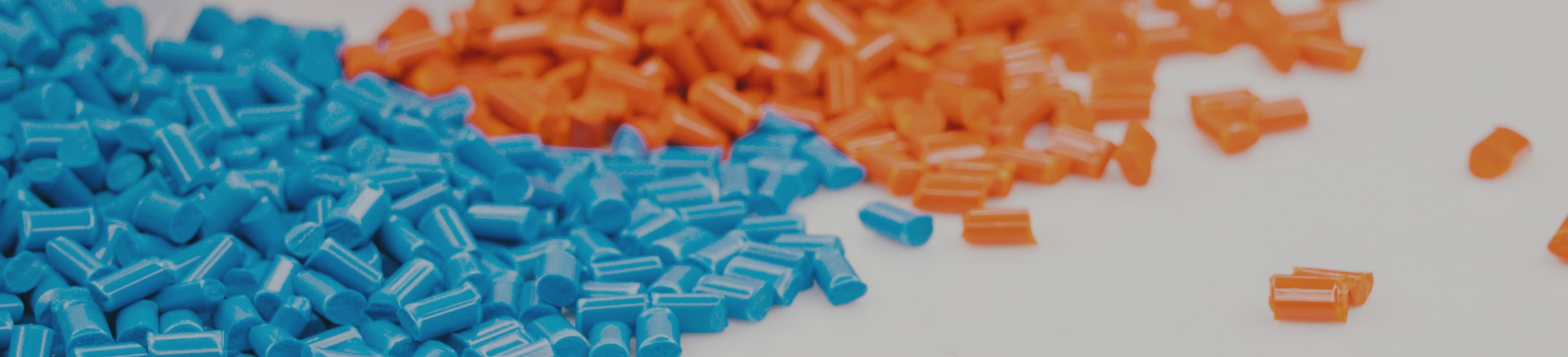
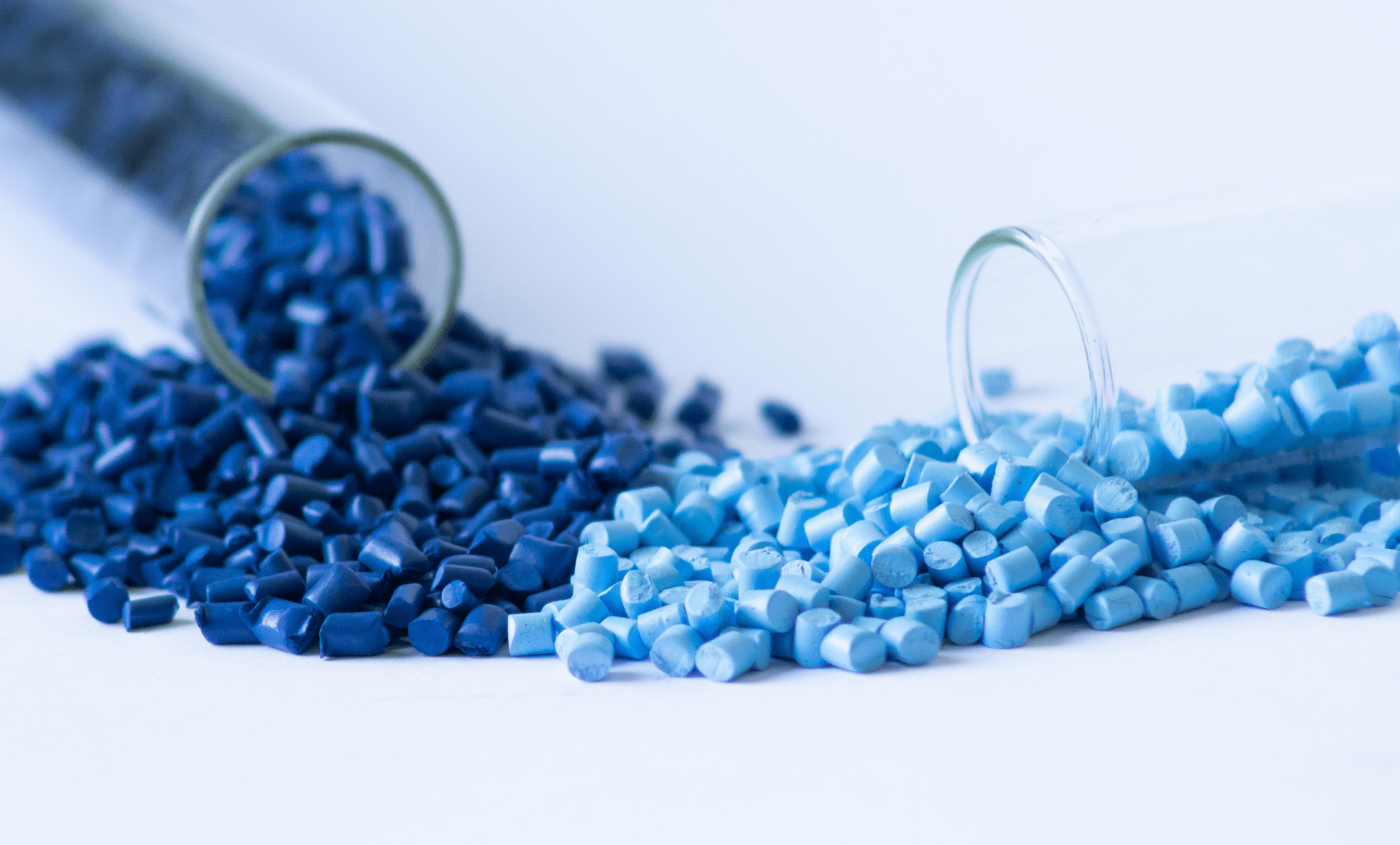
特徴
テクニカルデータシート
ご使用のアドバイス
ポリカーボネート(PC)樹脂の成形と乾燥条件
ポリカーボネート樹脂(PC樹脂)は、一般的な熱可塑成形方法(射出成形、射出圧縮成形、押出成形、ブロー成形、引き抜き(プルトルージョン)成形など)により成形されます。代表的な成形方法は射出成形です。PC樹脂の高分子連鎖がカーボネート結合を含んでいるため、水分と共に加熱されると加水分解を起こして、物性、特に分子量の低下に伴う衝撃強度の低下が見られるほか、外観的にも銀条(シルバー)や空隙(ボイド)などが発生するため、成形前には乾燥が必要です。具体的には、ペレット中の吸水率を0.015~0.020%以下とするために、120℃で4~5時間以上の熱風乾燥が推奨されます。
ポリカーボネート(PC)と他の透明材料との比較
ポリカーボネート樹脂(PC樹脂)を汎用の透明材料である無機ガラスに比べると、硬度、弾性率、耐熱性、耐溶剤性等においては劣りますが、比重が小さい、射出成形や押出成形により簡単に成形できる、簡単には割れない、着色が容易、といった樹脂ならではの利点があります。
一方、代表的な透明樹脂であるアクリル樹脂(PMMA樹脂)との比較では、下表に示す通り、PC樹脂は耐衝撃性・耐熱性・吸水率(吸水による寸法変化の指標)、更には自己消火性において勝りますが、高度の透明性という点ではPMMA樹脂が優れています。
また、PC樹脂はベンゼン環を分子構造中に有する(近紫外光を吸収する)ため日光など紫外線を含む光への長期曝露により黄ばみや脆化を生じる場合があります。更に、成形条件によっては光学的異方性が顕著に現れる、カーボネート結合(-OCOO-)を高分子連鎖の繰返し単位(モノマー単位)構造中に有するためアルカリ性や湿熱条件での使用では加水分解による性能低下が生じる場合がある、といった点にも注意が必要です。
樹脂 | 耐衝撃性 (J/m) | 耐熱性 (℃) | 吸水率 (%) |
---|---|---|---|
PC樹脂 | 640~960 | 121~132 | 0.15 |
PMMA樹脂 | 11~21 | 68~100 | 0.1~0.4 |
耐衝撃性:アイゾット衝撃強度 ASTM D256A (1/8インチ厚、ノッチ付)
耐熱性:荷重たわみ温度 ASTM D648 (1.82MPa荷重)
吸水率:ASTM D570 (24時間、1/8インチ厚)
出典: プラスチックポケットブック(㈱工業調査会、2003年全面改定版)
ポリブチレンテレフタレート(PBT)樹脂の乾燥性条件について
ポリカーボネート樹脂(PC樹脂)の射出成形の条件要素ごとに、基本的な考え方をご説明します。
- 成形温度:一般的には260~320℃に設定します。成形温度が高くなるほど溶融した樹脂の流動性が向上するので金型への充填性(特に薄肉部への充填性)は良くなります。その反面、成形サイクル、つまり樹脂のシリンダー内の滞留時間を考慮すべきで、滞留を極力短くして樹脂の熱劣化を最小限とすることも必要です。
- 成形圧力:射出圧力や保持圧力は成形品にヒケ(冷却時の収縮でへこみが生じる現象)やボイド(成形品中の空隙)等が発生しなければできるだけ低めに設定する方が良いですが、逆に、ある程度圧力を高めないと溶融した樹脂の流動性が不十分となるため金型内を満たし得ない現象が起きます。良い成形品を得る観点からは、成形収縮(金型の寸法に比べて成形品が収縮して小さくなる現象)を小さくするためには成形圧力を高めにし、逆に成形品に残る歪の低減や離型性確保の観点からはできるだけ低圧に設定することが望まれます。
- 射出速度:射出速度を大きくすると流れ距離が大きくなります。従って、成形品の厚みが薄くなるほど大きな射出速度が必要となりますが、反面、フローマーク(成形表面に残る流れ跡)やバリ(金型の隙間に樹脂が薄くあふれ出る現象)の発生などの不良を起こしやすくなります。成形品の形状に応じた射出速度の多段階コントロールにより、充填性と表面外観の両方を制御することが必要となります。
- 金型温度:PC樹脂の射出成形における金型温度は70~120℃が標準的です。金型温度が低いと、充填不足、フローマークなど外観不良の他、成形歪(成形品内部に残留する歪。これが大きい箇所は機械的強度の低下や光学的な不均一性の原因となります。)が発生しやすくなります。逆に高すぎると金型表面と密着しやすくなるので、離型不良や離型後の変形を起こしやすくなります。
以上ご説明した成形条件要素のいずれにおいても相反する要因がありますので、成形品の用途や性能に応じた形状や寸法の工夫と金型設計(例:流路設計、成形収縮の考慮など)が望まれます。
詳しくは弊社Websiteに掲載している詳細な技術資料をご参照ください。また、製品や金型設計の支援技術として,射出成形品の設計に広く取り入れられているCAE(Computer Aided Engineering)についてもお問い合わせ下さい。
ポリカーボネート(PC)成形品における割れの原因
弊社が把握して参りましたポリカーボネート樹脂(PC樹脂)成形品の割れトラブルの原因は、概ね、成形時の分子量低下(40%)、薬品との接触(40%)、経時劣化(10%)、デザインや設計の不適切(5%)、その他(5%)に分類されます。以下、主な要因をご説明いたします。
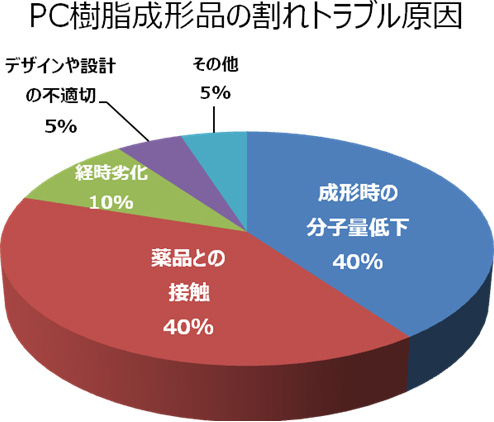
- 成形時の分子量低下:材料の乾燥不足、成形機のシリンダー内滞留による劣化(成形機・成形条件の選定不良を含む)、異樹脂の混入、等。
- 薬品との接触:油、グリース、印刷インキ、塗料、シンナー、アルカリ性薬品、等。内、アルカリ性薬品、アルコール類、高温のフェノール類は高分子連鎖のカーボネート結合を切断して分子量の低下を引き起こします。また、芳香族炭化水素(ベンゼン、トルエン、キシレン等)と塩素系炭化水素(塩化メチレン、クロロホルム等)によりPC樹脂は膨潤又は溶解します。
- 経時劣化:高温高湿雰囲気や蒸気との長時間接触、耐候劣化、熱衝撃(急激な温度変化)、等。
- デザインや設計の不適切:鋭利なエッジ部への応力集中、インサート部の応力、ウェルド部(別流路の溶融樹脂どうしの合流部分。一般的に強度が下がる箇所)への応力、等。
ポリカーボネート樹脂(PC樹脂)の成形歪みの影響と対策
一般に射出成形品では、ゲート(流路から成形品本体に樹脂が流入する入口部分)の近傍、成形品のエッジ部、製品の肉厚変化の大きい部分などにおいて残留歪が大きいことが経験的に知られています。ポリカーボネート樹脂(PC樹脂)は溶融流動性が比較的悪い材料であるため、この点に注意が必要です。また、非晶性樹脂であるため、成形品の残留歪が大きい箇所に、油脂類、インキや塗料、シンナー等の溶剤などが接触するとクラック(Crack;亀裂)を生じる原因となります。
成形品の残留歪をとり除く手段として、PC樹脂のガラス転移温度(Glass transition temperature;Tgと略記。約145℃)より20℃程度低い温度で加熱してその温度のまま一定時間保持し、その後室温まで除冷する操作が有効です。これを一般にアニール(Anneal;焼きなまし)処理と言います。弊社PC樹脂製品の場合、アニール条件としては温度120~125℃で1~2時間程度が標準です。考え方としては、単純な形状で肉厚が薄い成形品では短時間で良いですが、複雑な形状または肉厚が厚い場合は2~3時間アニール処理をすることもあります。
ポリカーボネート樹脂(PC樹脂)の再生・再利用
弊社のポリカーボネート樹脂(PC樹脂)製品の再生材使用につきましては、新材に対して20~30%混合して使用する方法が推奨されます。再生材の割合が大きくなるにつれて、若しくは再生を繰り返すにつれて、分子量の低下、黄変度の増加、全光線透過率等の低下が顕著となります。また、ガラス繊維等の強化材(フィラー)を含む強化グレードの場合,再生を繰り返すことによってこうしたフィラーが破砕するため、機械的強度が低下します。
【解説】結晶性樹脂と非晶性樹脂の特徴について
(1)高分子における結晶化とは
高分子(ここでは原理説明のために線状高分子を前提とします。)の結晶化とは、低分子の結晶(例:砂糖)やイオン性物質の結晶(例:食塩)では分子又はイオンが規則的に並んで結晶を構成する現象(図1参照)であるのに対して、ある与えられた条件、例えば、射出成形における溶融状態からの冷却条件、あるいは溶液状態からの濃縮条件等の下で、鎖状の高分子の一部が集合して部分的に同一方向に並んだ束を構成する現象(図2参照)です。また、高分子が結晶化を起こす場合、こうした結晶領域以外の不定の分子配置をとる非晶領域が通常共存します。
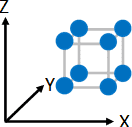
青色は分子又はイオンを、灰色は結晶格子(仮想的な概念)を、それぞれ表す。
X, Y, Z軸方向に、同一の結晶格子が規則的に続く。
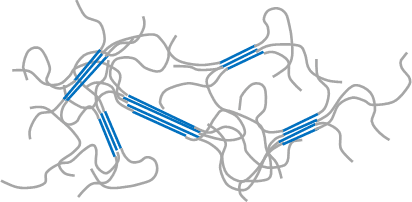
青色は結晶領域を、灰色は非晶領域を、それぞれ表す。
結晶領域では、高分子鎖が同一方向の束をなす。
非晶領域では、高分子鎖は不定の配置をとる。
いずれの結晶化も、分子、イオン又は高分子連鎖の繰返し単位(モノマー単位)が、分子間力やイオン結合を駆動力として熱力学的に最も安定な配置をとろうとする現象である点が共通しています。しかし、高分子の場合は、モノマー単位が高分子連鎖で束縛されているため重合される前のモノマー(低分子)よりも自由な配置をとる可動性が低下している点が本質的に異なっています。この高分子特有の分子の可動性低下が、非晶領域が残る原因です。更に、結晶領域の比率(「結晶化度」)や個々の結晶領域の大きさ(「結晶サイズ又は結晶子サイズ」)は成形条件に大きく依存するものとなります。
高分子の溶融又は溶液状態では高分子鎖は基本的に非晶性ですが、冷却や濃縮が進むにつれて、分子間力(引力)の効果が顕著となるので結晶化が進みます。但し、高分子の溶融又は溶液状態のいずれにおいても、冷却や濃縮が進むにつれて、低分子の系に比べて粘度が極めて大きくなるというもう1つの特徴があります。この粘度増大の効果により、結晶化が進む前に固化してしまうことが現実には生じます。従って、一般に、ゆっくりとした冷却や濃縮により、高分子鎖が再配置する時間を長くとることにより、結晶化度は高まります。ポリカーボネート樹脂(PC樹脂)やポリフェニレンエーテル樹脂(PPE樹脂)のような非晶性樹脂は、結晶化が遅いので非晶性のまま固化しやすい材料と理解できます。
(2)高分子の結晶領域の性質
結晶領域は強い分子間力による稠密な構造を有するため、一般に非晶領域に比べて、高い熱軟化温度と弾性率、低い線膨張係数と吸水率(即ち、温度と湿度による寸法変化の低下)を示します。この内、熱軟化温度については、非晶領域ではモノマー単位構造の剛直性(分子構造の可動性又は柔軟性の小ささ)に相関するガラス転移温度(Glass transition temperature;Tgと略記)にほぼ一致するのに対して、結晶領域ではTgよりも高温である融点(Melting temperature;Tmと略記)に一致します。
従って、樹脂成形品においては、一般に結晶化度を増大させると上記の物性については好ましい方向に動きます。但し、非晶領域中に分散している結晶領域は、弾性率の差に起因して外力による応力集中点として働くので、一般に結晶化度の増大により樹脂成形品の靱性は低下し脆化の方向に動きます。また、靱性は、結晶化度が同じ場合、結晶サイズを小さくすることにより改善されます。
(3)高分子の非晶領域の性質
樹脂成形品における非晶領域は、硬くて熱軟化しにくい結晶領域をいわばフィラー(Filler;充填される強化材)として含有するマトリックス(Matrix;連続相)として機能します。非晶領域の熱的性質は前記Tgに支配されますが、機械的物性に関しては靱性(強靭さ)を理解することが重要です。
Tgよりも低温においては、外力(引張り・曲げ・圧縮・ねじりなどの応力、重力による自重変形)を受けた非晶領域は、まず可逆的な弾性変形を生じます。これは、外力を除去すれば復元する範囲の比較的小さな変形であり、無機ガラスのように硬く脆い材料においても観察される現象です。しかしながら、靱性とは、弾性変形を超える大きく非可逆的な変形(塑性変形)をどの程度許すかに依存しています。こうした塑性変形の本質は、粘性流動、即ち、互いに絡み合った高分子鎖が非可逆的にずれながら配置を少しずつ変えることにより外力のエネルギーを熱として散逸し、材料全体として破断に耐えて変形していく過程です。
塑性変形が破断に至るきっかけは微小なクラック(亀裂)又はボイド(空隙)の発生です。理想的な非晶領域、つまり異物や不均質構造(結晶領域や粗密のゆらぎ)など応力集中要因を含まない場合を仮定すると、クラック又はボイドの発生原因として、①高分子末端、②高分子鎖の絡み合いのほどけ、③高分子鎖の切断の3つが考えられ、いずれも変形の途上で分子レベルの非常に微小なボイドの発生源となります。これら3要因の内、①と②は分子量が大きいほど抑制されます。これは、分子量が大きいほど(長いほど)単位重量当たりの分子末端数は減少し、かつ、絡み合いはほぐれにくくなるためです(例:ゆで上がった麺が長いほど全体としてほぐれにくくなることから類推できます)。つまり、分子量が大きいほど靱性的には有利になります。
上記③の高分子鎖の切断については、上記②の絡み合いの観点とも関連しますが、高分子鎖の硬さ(モノマー単位構造の剛直性)が1つの要因となります。つまり、高分子鎖が柔軟な場合、互いの絡み合いを解消することなく全体としての変形に追随しやすいですが、剛直な場合は可動性が低下するので変形に追随できずに絡み合い点に応力が集中しやすくなる結果、高分子鎖の切断が生じやすくなると考えられます。高分子鎖の剛直性は、これが大きいほど非晶領域の弾性率は増大する、熱的性質としては前記Tgを上昇させる(熱軟化温度を高める)が溶融流動性の低下(溶融粘度が上昇し成形性悪化)をもたらす、溶融流動性を高めるために分子量を小さくすれば前記の通り靱性的には不利になる、といった実用的に相反する複雑な挙動を引き起こす要因といえます。
(4)結晶性樹脂と非晶性樹脂
線状高分子は、冷却や濃縮の条件を選べば結晶化する能力を基本的に持っています。しかしながら、通常「結晶性樹脂」とは、射出成形や押出成形などの通常の成形条件において、実用的に好ましい物性バランスを示す程度に結晶化が進行する樹脂を意味します。逆に「非晶性樹脂」とは、そうした成形条件において結晶化がほとんど進行しない樹脂を意味します。
「結晶性樹脂」であるエンプラとしては、ポリアミド樹脂(PA樹脂)、ポリアセタール樹脂(POM樹脂)、ポリブチレンテレフタレート樹脂(PBT樹脂)、ポリエチレンテレフタレート樹脂(PET樹脂)、ポリフェニレンサルファイド樹脂(PPS樹脂)等が挙げられ、溶融流動性及び耐薬品性が良好、ガラス繊維等のフィラーによる補強効果(弾性率、強度、耐熱性を向上する効果)が大きい、といった特徴を持ちます。
「非晶性樹脂」であるエンプラとしては、ポリカーボネート樹脂(PC樹脂)、ポリフェニレンエーテル樹脂(PPE樹脂)、ポリアリレート樹脂(PAR樹脂)等が挙げられ、透明性を有する、異方性と成形収縮が小さい、といった特徴を持ちます。